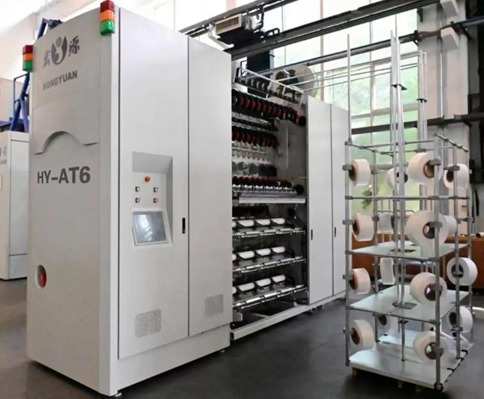
The HY-AT6 air texturing machine is an advanced piece of chemical fiber equipment designed for processing nylon FDY filaments using compressed air jet technology. It excels in producing high-quality air-textured yarns (ATY) efficiently and at high speeds. This machine is crucial for post-processing in the chemical fiber industry, especially when spinning high value-added products.
Promoting Green and Low-Carbon Innovation
This machine plays a significant role in driving the textile and chemical fiber industries toward greener and low-carbon operations. It achieves this by enhancing energy efficiency, integrating intelligent management systems, and embracing environmentally friendly design and manufacturing practices. Its modular architecture not only simplifies maintenance and upgrades but also reduces energy consumption and emissions throughout the production process.
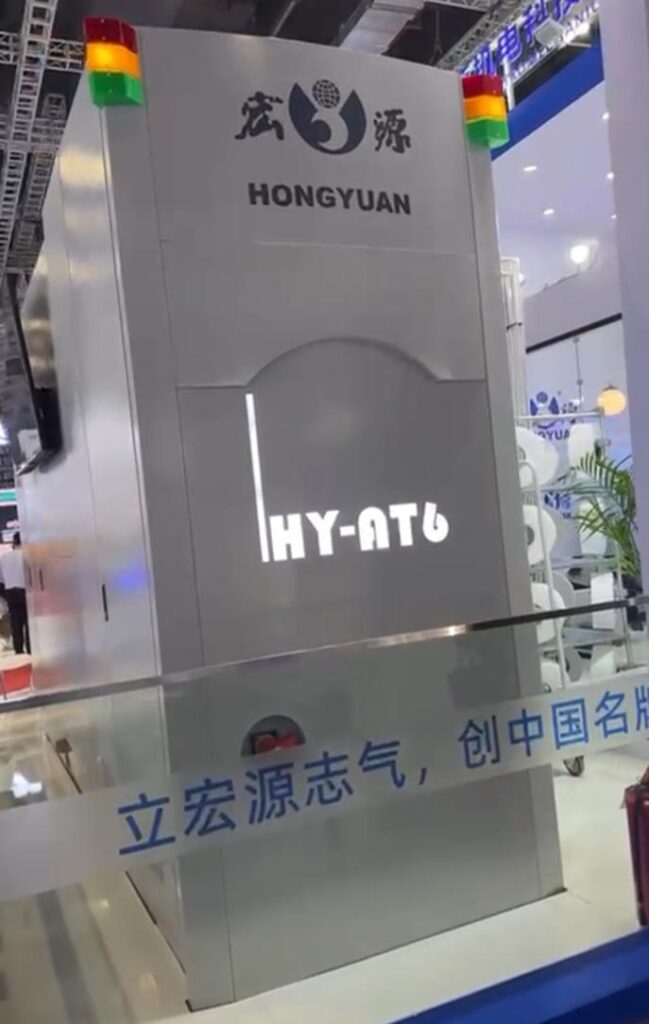
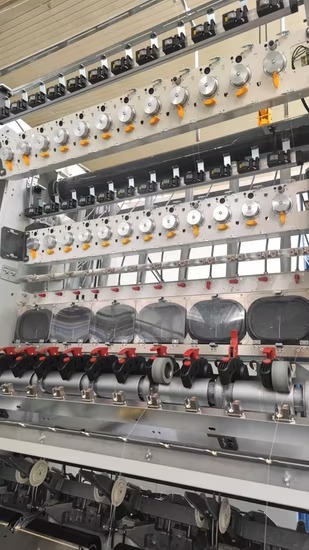
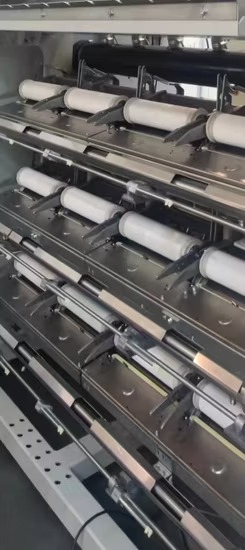
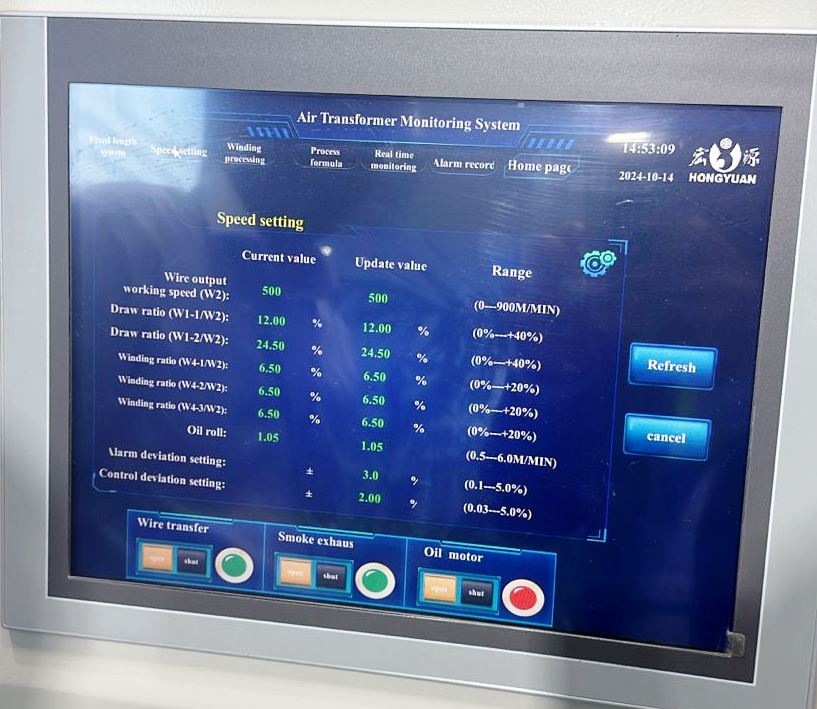
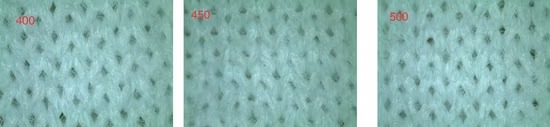
Eco-Friendly Design and Manufacturing
- Precision Moistening System: Equipped with a precisely controlled moistening system, the machine effectively contributes to carbon reduction goals.
- Advanced Nozzle Technology: The use of optimized nozzles extends cleaning intervals, enhances the range and reliability of process adjustments, and lowers gas consumption.
- Innovative Air Deformation Wire: Incorporating a leading-edge air deformation wire significantly boosts nozzle deformation efficiency, reduces gas usage, and enables high-speed, efficient operation, thereby cutting down energy consumption and carbon emissions.
- Energy-Saving Motors: Through technical upgrades, the transmission system now utilizes more efficient and energy-saving motors.
High Degree of Intelligence
The machine features advanced intelligent control systems that provide real-time monitoring and management. It can automatically adjust operational statuses and equipment parameters based on production demands, further minimizing carbon emissions. By leveraging big data analytics, the system deeply analyzes operational data to uncover potential areas for energy savings and consumption reduction, enabling the formulation of targeted optimization strategies.
Superior Speed, Efficiency, and Quality
To maximize production efficiency, the machine adopts internationally acclaimed single-spindle electronic precision digital winding technology. This single-motor, high-speed precision winding system replaces traditional mechanical grooved drum winding devices, resulting in a simplified structure. It offers flexible geometric forming and precise winding tension control, which enhances the quality of package unwinding, dyeing, and weaving processes.